Wheel building question.
#26
Senior Member
One other thing to consider, you can get larger spokes.
A couple of brands offer 2.3mm straight gauge spokes. Sapim & Pillar. Others?
I thought there were 2.3/2.0 double butted spokes, but they appear to be single butted (thick at the J-bend, thin at the threads).
Make sure you buy name brand spokes. DT, Sapin, Maybe Pillar.
You might have to touch up some of the holes in the rims & hubs.
A couple of brands offer 2.3mm straight gauge spokes. Sapim & Pillar. Others?
I thought there were 2.3/2.0 double butted spokes, but they appear to be single butted (thick at the J-bend, thin at the threads).
Make sure you buy name brand spokes. DT, Sapin, Maybe Pillar.

You might have to touch up some of the holes in the rims & hubs.
i had to set a high DS tension so that the lowest NDS spoke is just a bit lower than 100kgf - with the tire uninflated, that is.
i could afford all this after achieving good radial true balanced with uniform tension so YMMV.
#27
Senior Member
Thread Starter
Hang on...
Put the brakes on this....

Can you post another photo of the direct side view of the wheel & spokes?
Are the spokes bending side-to-side, or bending inline with the wheel?
The 1x, 2x, 3x, 4x issue primarily has to deal with bends inline with the wheel (front and back).
From your photo, it looks like the bends are side-to-side with a rim with either eyelets or sockets.
That is a completely different issue.
Your IGH hub may have wide flanges as there is less of a need to deal with dishing (and more gears inside).
I can't see an assembly problem from the photo. The eyelets appear to be centered. However, with some wheels, there is an assymetry to the spoke hole drilling. So, if one puts a spoke in the spoke hole loosely and lets it hang, it will have a preference for one side or the other. And every other spoke should have a preference to hang in the opposite direction.
So, a few possibilities:
Put the brakes on this....

Can you post another photo of the direct side view of the wheel & spokes?
Are the spokes bending side-to-side, or bending inline with the wheel?
The 1x, 2x, 3x, 4x issue primarily has to deal with bends inline with the wheel (front and back).
From your photo, it looks like the bends are side-to-side with a rim with either eyelets or sockets.
That is a completely different issue.
Your IGH hub may have wide flanges as there is less of a need to deal with dishing (and more gears inside).
I can't see an assembly problem from the photo. The eyelets appear to be centered. However, with some wheels, there is an assymetry to the spoke hole drilling. So, if one puts a spoke in the spoke hole loosely and lets it hang, it will have a preference for one side or the other. And every other spoke should have a preference to hang in the opposite direction.
So, a few possibilities:
- Wheel assembled backwards, and right spoke holes going to left spokes.
- Eyeletted spoke holes are straight and don't let nipples go to the side enough.
- Oversized nipples exacerbating the problem above.
I can say looking at the side, the spokes look straight. The bend is pointing out.
The wheel is assembled correctly and not backwards. The holes that point to one hub side go to that side. I verified that with one of the broken spokes. This guy does know how to build wheel, he's just not that familiar with building larger utility wheels with an IGH.
The nipples themselve almost don't move in the hole. They can't really point as far out as needed which is the problem and why the spokes are breaking at the nipple. The wheel is built with thicker spokes (~2.5mm).
#28
Senior Member
Join Date: Nov 2014
Location: Eugene, Oregon, USA
Posts: 27,547
Mentioned: 217 Post(s)
Tagged: 0 Thread(s)
Quoted: 18378 Post(s)
Liked 4,512 Times
in
3,354 Posts
I can say looking at the side, the spokes look straight. The bend is pointing out.
The wheel is assembled correctly and not backwards. The holes that point to one hub side go to that side. I verified that with one of the broken spokes. This guy does know how to build wheel, he's just not that familiar with building larger utility wheels with an IGH.
The nipples themselve almost don't move in the hole. They can't really point as far out as needed which is the problem and why the spokes are breaking at the nipple. The wheel is built with thicker spokes (~2.5mm).
The wheel is assembled correctly and not backwards. The holes that point to one hub side go to that side. I verified that with one of the broken spokes. This guy does know how to build wheel, he's just not that familiar with building larger utility wheels with an IGH.
The nipples themselve almost don't move in the hole. They can't really point as far out as needed which is the problem and why the spokes are breaking at the nipple. The wheel is built with thicker spokes (~2.5mm).

It sounds like part of the problem is using oversized spokes/nipples with the eyelets, and the oversized nipples aren't tilting as much as one might otherwise expect.
It should be reasonably quick and easy to choose an electric drill with a bit sized for the nipples, and hand-ream every spoke hole to the approximate size/angle that is needed, although I don't know if the eyelets would cause a problem. But, worst case, they'd just act like nipple washers.
#29
Senior Member
if spokes are having a large bend at the nipple because of the large flange of the hub and the 3x pattern then a solution to prevent spokes breaking at the nipple would be to properly bed in the nipples in the eyelets and also cause a permanent twist of the spokes at the nipple. it's called stress relieving.
Likes For adipe:
#30
Senior Member
Thread Starter
if spokes are having a large bend at the nipple because of the large flange of the hub and the 3x pattern then a solution to prevent spokes breaking at the nipple would be to properly bed in the nipples in the eyelets and also cause a permanent twist of the spokes at the nipple. it's called stress relieving.
#31
Senior Member
i can't see right now how a particular rim would prevent the nipples from aligning better.
i don't know too much about polyax nipples etc.; they could be of use but i'm not sure, haven't worked with them. they are advertised to press more evenly on the eyelets but i doubt (at the moment) it could mitigate all the problems of having a very shallow angle (much less than 90 degrees) between the rim and the spoke direction.
you need to stress relieve properly as to raise the tension of the spokes to about (i went even over 200kgf but that's another matter, YMMV) for other different reasons.
i would advise to raise the tension to even more than 150kgf after being careful to wax lubricate the nipples and the spokes thread as to insure a friction of even less than 0.1 coefficient. and - i can't stress this point more than enough as it is of so much importance - dial in the radial true with spoke tension variance on the drive side when the NDS are slack and DS spokes are at a medium tension. in my case it was about 70kgf. and if there is more than 0.3mm lateral runout with NDS spokes being slack you could consider adjusting the NDS spokes but this will complicate the measurements, computing or just estimating the balancing of tension variance with radial runout.
so, after you adjust DS spokes at that medium tension in order to not need to touch them again... raise the NDS tension to increase overall tension and indirectly get average DS to high levels (say 150kgf, or even more) then you could grab parallel spokes in your hands and do the stress relieving but be sure to not have residual twist in neither DS nor NDS spokes when you do it. put labels on DS spokes to finish the radial and tension variance tuning from the get go with the labels finishing at being all in the same positions (angle) you put the labels, that being when the spokes had no tension in them. it is of much benefit to the wheel to insure low elastic twist in the spokes for several reasons and it's not a much consuming time stage to do it. mark numbers on them as it will help you keep track on them for measurements and adjusting as well.
you may consider going with a 2x pattern for large flanges hubs. you might mix a 2x DS with a 3x NDS so that the NDS spokes would vary less in tension from disc braking or the torque generated by you pedaling and a high torque motor. the benefit of using 2x DS would be that the high tensioned spokes don't get a large tension +/- when under torque and dynamic loads. habits as to learn to avoid torque by pedaling and braking when dealing with potholes are of use.
i am very happy with a 2x pattern on both flanges but then again... that is because i fixed the wheel by straightening the rim (by plastic deformation after it was bent out of shape) - i have not chosen the spokes setup but adapted to it. the only significant advantage of using the same thick spoke morel (DT Alpine) on both flanges is that they are able to sustain impacts with object hitting the spokes with much larger speed and/or larger mass.
i don't know if previous owners replaced the spoke, i doubt they ever broke. stress relieving achieves spoke permanent bend at the nipples and i guess the factory (KTM) had done an good enough job for that purpose. but i also point out that the setup was both 2x on both flanges.
the last owner had no success in truing the wheel wherever he went to service it. i haven't talked to the guy too much, he was the kind to hide any blame. for example he claimed that if the one of the bolt had stripped in the brake post mount threads of the frame it was a problem the bike had not had prior to me buying it. and i had not torqued the bolt but unscrewed it and had this surprise. the bolt was short and engaged only two threads!
so, given the all too common lack of quality service around... i chose to put into the practice the skills and knowledge i achieved before and after repairing properly the only other wheel i worked with 5 years ago. i had changed the nipples from DT Prolock (aluminum with loctite-like paste inserted in them) for the DT Rev (1.5mm) spokes to be able to be under just a tad less than 120kgf tension for a rim brake front wheel with a DT TK540 rim. shame on KTM for picking those nipples, i highly doubt there were a replacement done. the tension was all over the place, the rim had significat radial runout and the average tension was about surely no more than 80kgf.
so i know my facts and i also practiced. feel free to seek other people's opinions but also try to learn a bit about how stuff works.
https://en.wikipedia.org/wiki/Strength_of_materials
#32
Senior Member
... you could use this rim you have for practice if you feel you would risk things when building on a new rim.
i would advise to change the spokes too for a new rim or for different spoke cross etc. dunno about what gauge you would choose but be sure to pay attention to spoke being vulnerable to plastic deformation by torsion. butted spokes more so.
https://www.tribology-abc.com/calculators/e3_6a.htm
i would advise to change the spokes too for a new rim or for different spoke cross etc. dunno about what gauge you would choose but be sure to pay attention to spoke being vulnerable to plastic deformation by torsion. butted spokes more so.
https://www.tribology-abc.com/calculators/e3_6a.htm
#33
Generally bewildered
Join Date: Aug 2015
Location: Eastern PA, USA
Posts: 3,037
Bikes: 2014 Trek Domane 6.9, 1999 LeMond Zurich, 1978 Schwinn Superior
Mentioned: 20 Post(s)
Tagged: 0 Thread(s)
Quoted: 1152 Post(s)
Liked 341 Times
in
251 Posts
Jobst Brandt (in his book "The Bicycle Wheel" recommended for folks seriously interested in how bicycle wheels work) addressed the issue of the rim holes not allowing the nipples to swivel enough. He suggested bending the spoke so that the nipple beds properly in the frame, but there is no residual bending stress in the spoke. If you have bending stress, you have the possibility of stress reversal and premature fatigue failure. See pic below.
Sapim makes PolyAx(R) nipples that claim to have a wider range of alignment. Might help - haven't used them, but some folks here swear by them.
Strongly agree with OneIsAllYouNeed (at least on the OP's topic - clearly you need more than one!) regarding butted spokes. Butted spokes allow the spoke to stretch more, and when the rim is deflected, the spoke remains stressed over a wider range. There is no stress reversal. In the other direction, if the spoke is stretched more, the spring force of the butted spoke is lower and doesn't transmit the high force to the nipple or j-bend that a straight gauge spoke would.
Or, find a rim that allows more spoke swivel.
Sapim makes PolyAx(R) nipples that claim to have a wider range of alignment. Might help - haven't used them, but some folks here swear by them.
Strongly agree with OneIsAllYouNeed (at least on the OP's topic - clearly you need more than one!) regarding butted spokes. Butted spokes allow the spoke to stretch more, and when the rim is deflected, the spoke remains stressed over a wider range. There is no stress reversal. In the other direction, if the spoke is stretched more, the spring force of the butted spoke is lower and doesn't transmit the high force to the nipple or j-bend that a straight gauge spoke would.
Or, find a rim that allows more spoke swivel.
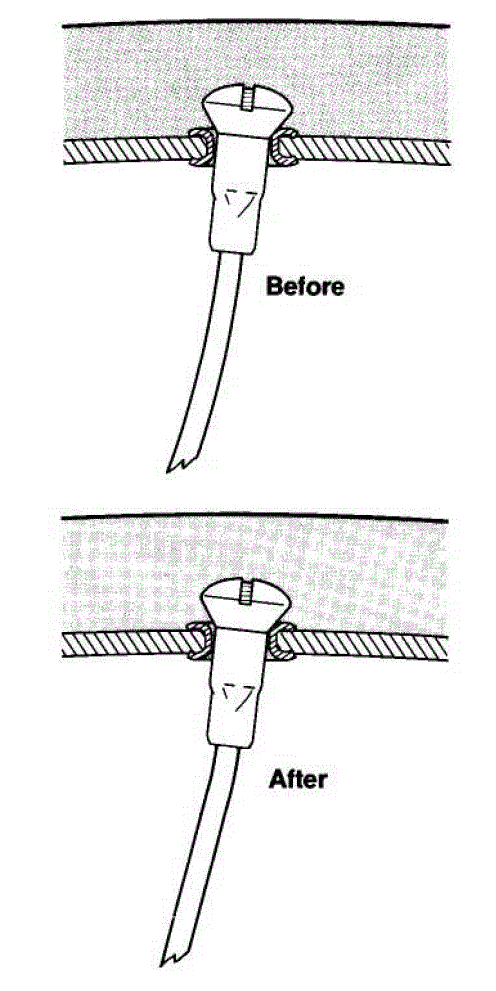
Last edited by WizardOfBoz; 08-30-19 at 06:19 AM.
#34
aged to perfection
Join Date: Jun 2009
Location: PacNW
Posts: 1,817
Bikes: Dinucci Allez 2.0, Richard Sachs, Alex Singer, Serotta, Masi GC, Raleigh Pro Mk.1, Hetchins, etc
Mentioned: 24 Post(s)
Tagged: 0 Thread(s)
Quoted: 838 Post(s)
Liked 1,258 Times
in
663 Posts
what Boz said above is exactly right. Just take your Mark 1 pliers and tweak the spoke. Don't worry, the 3-5 degree bend won't hurt a thing,
That's the fix
Mark Petry
Bainbridge Island, WA USA
That's the fix
Mark Petry
Bainbridge Island, WA USA
#35
Senior Member
i would rather bend the spoke indirectly by raising the tension to a much more high level...
you can't be that precise using pliers to bend the spokes right where it's needed.
also, the spokes should have residual compressional stress on the surface from the factory. when you use the pliers you screw up the spokes surface.
wheelbuilding is to be done as a whole process. don't just pliers and make bends in the spokes,
achieve the best radial true as possible on the DS spokes when NDS are slack and then raise the NDS tension. lower the NDS tension after you perform all the plastic deformations that need to be done as to straighten the rim, bed in the flanges, bed in the nipples/eyelets AND bend in the spokes by that means.
i would go as high as 170-180kgf on the non drive side (therefore DS being just a little bit higher than NDS) as to indirectly raise by that means the DS tension. make sure lateral true at each stage so that you grab parallel spokes and squeeze them bringing them closer.
i squeezed spokes as hard as i could when they were at no more than 140kgf and i haven't achieved too much regarding straightening the rim. spokes (nipples) do not pull through the rim very easily this way but if you leave the wheel without a proper stress relieving job they will crack the rim due to creep deformation (in time) and stress corrosion cracking.
this is a proper job to be done if you have a rim that has eyelets and it is made of 6061-T6 or similar alloy.
you have be able to do some calculations and/or discern when the material (rim, nipples) is starting to give in as to back off from that point. spokes are designed to sustain much more tension than the levels they attain when in use but they can crack due to fatigue - fast and large amplitude strains when in low tension - or corrosion or residual bending (flexural) stresses near the nipples or at the flange. going a very high tension and backing off makes sure the material gets deformed and set in so that when you lower back the localized stresses are much lower.
every indentation on the surface creates what is called a stress riser and it makes matters worse. avoid using pliers on the spokes.
you may try using some plastics for bending the spokes but you only achieve one aspect to the whole job that needs to be done and you can't make the same precise bend as when going high tension and the backing off on a radial/tension tuned wheel.
you can't be that precise using pliers to bend the spokes right where it's needed.
also, the spokes should have residual compressional stress on the surface from the factory. when you use the pliers you screw up the spokes surface.
wheelbuilding is to be done as a whole process. don't just pliers and make bends in the spokes,
achieve the best radial true as possible on the DS spokes when NDS are slack and then raise the NDS tension. lower the NDS tension after you perform all the plastic deformations that need to be done as to straighten the rim, bed in the flanges, bed in the nipples/eyelets AND bend in the spokes by that means.
i would go as high as 170-180kgf on the non drive side (therefore DS being just a little bit higher than NDS) as to indirectly raise by that means the DS tension. make sure lateral true at each stage so that you grab parallel spokes and squeeze them bringing them closer.
i squeezed spokes as hard as i could when they were at no more than 140kgf and i haven't achieved too much regarding straightening the rim. spokes (nipples) do not pull through the rim very easily this way but if you leave the wheel without a proper stress relieving job they will crack the rim due to creep deformation (in time) and stress corrosion cracking.
this is a proper job to be done if you have a rim that has eyelets and it is made of 6061-T6 or similar alloy.
you have be able to do some calculations and/or discern when the material (rim, nipples) is starting to give in as to back off from that point. spokes are designed to sustain much more tension than the levels they attain when in use but they can crack due to fatigue - fast and large amplitude strains when in low tension - or corrosion or residual bending (flexural) stresses near the nipples or at the flange. going a very high tension and backing off makes sure the material gets deformed and set in so that when you lower back the localized stresses are much lower.
every indentation on the surface creates what is called a stress riser and it makes matters worse. avoid using pliers on the spokes.
you may try using some plastics for bending the spokes but you only achieve one aspect to the whole job that needs to be done and you can't make the same precise bend as when going high tension and the backing off on a radial/tension tuned wheel.
#36
Generally bewildered
Join Date: Aug 2015
Location: Eastern PA, USA
Posts: 3,037
Bikes: 2014 Trek Domane 6.9, 1999 LeMond Zurich, 1978 Schwinn Superior
Mentioned: 20 Post(s)
Tagged: 0 Thread(s)
Quoted: 1152 Post(s)
Liked 341 Times
in
251 Posts
adipe,
I agree about not adding stress risers. Jobst Brandt suggests squeezing adjacent spokes to put the small set in the spoke. I think you could use two pieces of wood stuck through the spokes, with two spokes in between the wood. Grasping both pieces of wood on either side of the rim and squeezing would get you the bend you want, with no risers.
They do (or at least did) make pliers that had flat mating pressure surfaces, with a groove in them. The ends of the groove were radiused. This allowed you to bend the spoke w/o scratching it.
I disagree regarding using greater spoke force to induce a bend. Spoke force high enough to induce an elastic deformation of the spoke will also probably be high enough to pull through the spoke holes or taco the rim. If you don't bend the spokes slightly, then the nipple is canted over and the sides are bearing on the sides of the hole - which itself is a stress riser. Eliminating those side forces on the spoke, nipple, and spoke hole was one objective of Brandt's suggestion. Adding spoke tension doesn't address the key issue. The 170-180kg force on a NDS you mention creates an enormous force on the rim holes and rim structure. You'd be dealing with 200kgf or more on the DS with proper dishing. That's too much for almost any rim. What rims did you lace this tight?
Is the reason you don't like the spoke bend mostly due to possible scratches/risers being created?
I agree about not adding stress risers. Jobst Brandt suggests squeezing adjacent spokes to put the small set in the spoke. I think you could use two pieces of wood stuck through the spokes, with two spokes in between the wood. Grasping both pieces of wood on either side of the rim and squeezing would get you the bend you want, with no risers.
They do (or at least did) make pliers that had flat mating pressure surfaces, with a groove in them. The ends of the groove were radiused. This allowed you to bend the spoke w/o scratching it.
I disagree regarding using greater spoke force to induce a bend. Spoke force high enough to induce an elastic deformation of the spoke will also probably be high enough to pull through the spoke holes or taco the rim. If you don't bend the spokes slightly, then the nipple is canted over and the sides are bearing on the sides of the hole - which itself is a stress riser. Eliminating those side forces on the spoke, nipple, and spoke hole was one objective of Brandt's suggestion. Adding spoke tension doesn't address the key issue. The 170-180kg force on a NDS you mention creates an enormous force on the rim holes and rim structure. You'd be dealing with 200kgf or more on the DS with proper dishing. That's too much for almost any rim. What rims did you lace this tight?
Is the reason you don't like the spoke bend mostly due to possible scratches/risers being created?
#37
Disco Infiltrator
Join Date: May 2013
Location: Folsom CA
Posts: 13,446
Bikes: Stormchaser, Paramount, Tilt, Samba tandem
Mentioned: 72 Post(s)
Tagged: 0 Thread(s)
Quoted: 3126 Post(s)
Liked 2,105 Times
in
1,369 Posts
If you were to build with fewer crosses could you run all the spokes inward at the flange and not have such a big angle from the vertical plane?
#38
working on my sandal tan
Join Date: Aug 2011
Location: CID
Posts: 22,629
Bikes: 1991 Bianchi Eros, 1964 Armstrong, 1988 Diamondback Ascent, 1988 Bianchi Premio, 1987 Bianchi Sport SX, 1980s Raleigh mixte (hers), All-City Space Horse (hers)
Mentioned: 98 Post(s)
Tagged: 0 Thread(s)
Quoted: 3871 Post(s)
Liked 2,568 Times
in
1,579 Posts
i would rather bend the spoke indirectly by raising the tension to a much more high level...
you can't be that precise using pliers to bend the spokes right where it's needed.
also, the spokes should have residual compressional stress on the surface from the factory. when you use the pliers you screw up the spokes surface.
you can't be that precise using pliers to bend the spokes right where it's needed.
also, the spokes should have residual compressional stress on the surface from the factory. when you use the pliers you screw up the spokes surface.
i would go as high as 170-180kgf on the non drive side (therefore DS being just a little bit higher than NDS) as to indirectly raise by that means the DS tension. make sure lateral true at each stage so that you grab parallel spokes and squeeze them bringing them closer.
#39
Senior Member
Thread Starter
Actually looking at the wheel again, there is a bend even when looking at the side of the wheel. So the spokes are bending both ways. I'm about to leave for the bike shop and have him rebuild it again. This time though I'm not really going to push on using larger spokes, but rather getting any spoke to work and be straight. Even smaller 1.8-2mm spokes should last years hauling heavy loads if properly installed. Typically I haul one heavy load a week (groceries). Anything really big and I use the trailer.
As I said, he clearly knows how to build a wheel as he built my front wheel and it's near perfect with less that a 5% difference between spoke tensions and the spokes do not bend. He has also built other wheels for me that outlasted the hub. It's likely the wider hub and taller flange that's causing the problem.
And the "grime" on the spokes is locktite. He figured the breaking spokes was caused by the nipples loosening. Clearly not the case as this wheel failed sooner than any other he has built.
As I said, he clearly knows how to build a wheel as he built my front wheel and it's near perfect with less that a 5% difference between spoke tensions and the spokes do not bend. He has also built other wheels for me that outlasted the hub. It's likely the wider hub and taller flange that's causing the problem.
And the "grime" on the spokes is locktite. He figured the breaking spokes was caused by the nipples loosening. Clearly not the case as this wheel failed sooner than any other he has built.
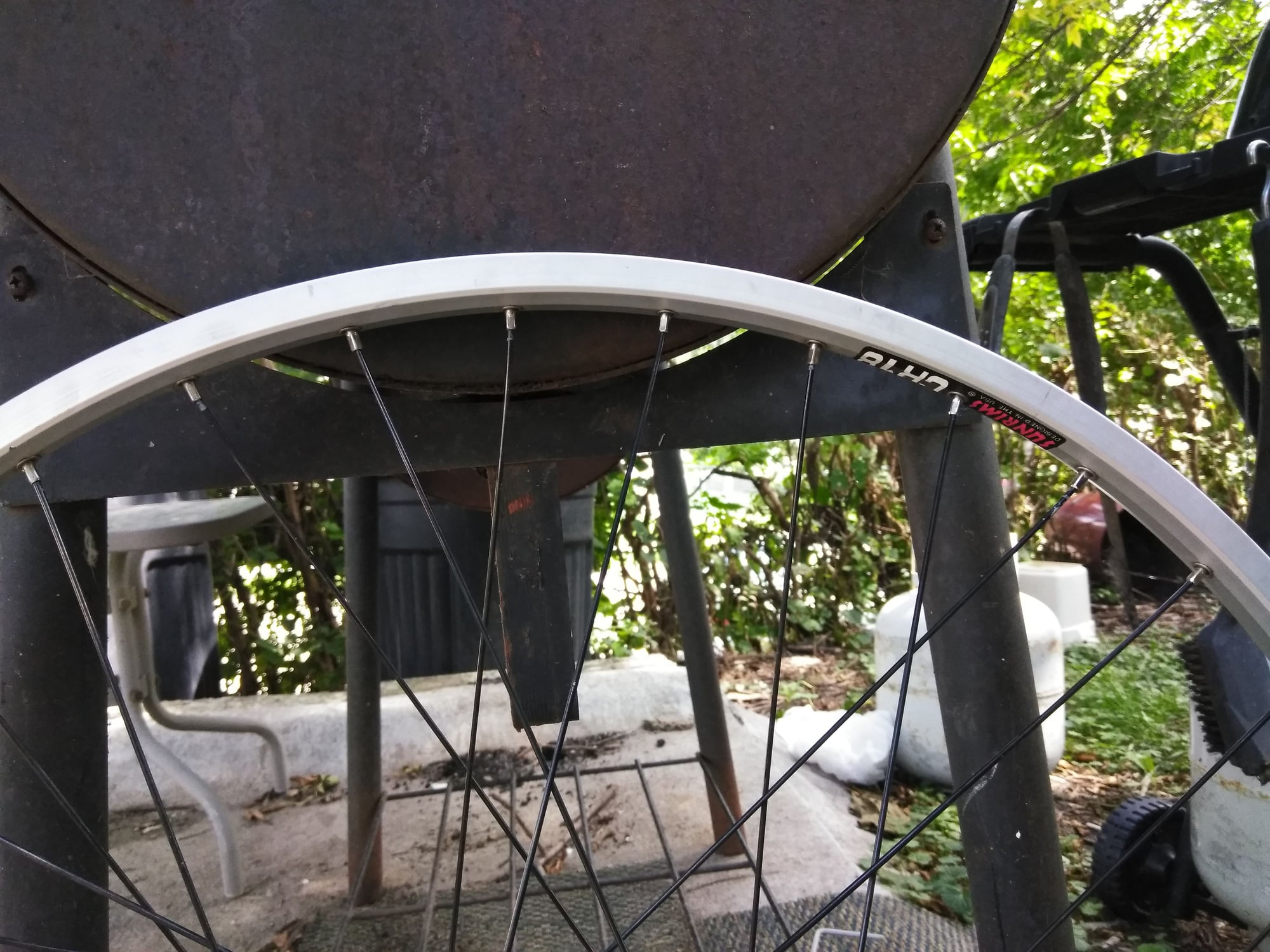
#40
Senior Member
Thread Starter
Dropped it off and made it clear I don't care how it's built other than I want a 2x lacing and I don't want to see bent spokes. He dug up a velo blunt rim. Said it retailed for $90 and discounted it to $60 for my trouble. It's a rim that does not have eyelets, so hopefully the nipples will be able to move freely (Which I pointed out could have been the issue with the other rim as the nipples on that one barely moved). So in about a week, or two I'll get the results. With luck it will last long enough for me to save some money and buy the parts to start building my own wheels.
#41
Steel is real
Geeze mate.. even my 4x patterns don't angle like that from the nipples. I wonder if those nipples are compatible to the rim eyelets?! they don't allow for them to angle accordingly.
#42
Steel is real
Maybe that rim is only intended for a radial pattern - front wheel?
#43
Senior Member
You don't need pliers to correct the spoke line. Just press on them with your fingers while the tension is still low. It's not rocket science.
You are free to do whatever you like with your wheels, but good luck with warranty claims if you go way over their max rating. 180kgf on the non-drive side is ridiculous, and should not be necessary on a properly spec'd wheel.
You are free to do whatever you like with your wheels, but good luck with warranty claims if you go way over their max rating. 180kgf on the non-drive side is ridiculous, and should not be necessary on a properly spec'd wheel.
you have to press really hard when grabbing parallel spokes at the middle.
for example... you can hardly break a wire when putting some heavy wet clothes at the extremity of the wire but you will be able to increase the wire's tension when you put the load at the middle of it. the same with the spokes being grabbed and pressed to the point when your hands hurt... at the middle of the spoke length.
this practice of squeezing spokes and not going higher tension than the ~120kgf (by nipple turning) is done by somehow lazy wheelbuilders or those who don't know the whole thing about the matter.
i was saying being able to achieve 180kgf tension that will not remain permanent. the NDS spokes would be brought back to the final tension after all this work.
and i am repeating that the radial and tension variance adjustments are to be done at a very accurate level at a medium tension (NDS being slack) for being able to work towards that high tension. i would recommend going to about 30% more than final tension only when being able to accurately balance the DS tension/runout and also make sure at every stage of raising NDS tension that the wheel can be laterally tuned to 0.1mm total runout.
then again... if you have less than 2mm spokes... YMMV. or if you can't achieve the final goal: +/-0.05mm radial and axial runout with +/-5% DS tension variance. the more you increase the NDS tension the more you should see you approach these figures and be able to continue. don't go crazy if you either can't measure this or if things don't progress towards this goal.
for example... i would never have NDS tension increased at more than 135kgf for 1.5mm spokes. that is because 1.5mm spokes can be permanently twisted at even less than 100kgf. only by temporarily lowering each spoke tension should you screw in the nipple can these spokes be tensioned safely and it's a very difficult thing to even achieve 135kgf for that matter. in other words rim straightening is a tedious job when using very thin spokes.
i am exposing the principles, more so than establishing hard figures. some people will never be able to figure out how to measure radial runout and doing the math etc. but at least they may understand what makes a durable wheel.
anyway, when you stress relieve the wheel by grabbing parallel spokes or pressing down on the axle with your weight you are supposed to achieve even higher tensions than 180kgf. going at this high tension by gradually tuning the NDS nipples will both work for stress relieving and for straightening the rim at a very precise level.
the rim has a fatigue limit and it can be improved upon by stress relieving. achieving low spoke tension variance means lower flexural stresses and better fatigue life. even a 2% strain cold work is not decreasing ductility too much and anyway, the alloy is already brought to a lower ductility - by tempering - than at the annealed state.
it's because of the fatigue limit being established at about 96.5 MPa that the tension they recommend is about 120kgf and also because spoke tension variance makes flexural stresses impose tensional strain on the rim around the nipples.
but the general tolerance of spoke tension variance is at +/-20% and that is enormous. then of course you will impose the 120kgf maximum spoke tension for that usage. if people don't finely tune radial runout with tension variance you impose that figure as a general recommendation and that is the end of the discussion with the general public. anything else becomes heresy for the general audience.
stress relieving achieves more than one purpose. one is lowering spoke tension variance by deforming the rim wherever it might out of the ideal shape. another is bedding in of the nipples/eyelets, flanges and making permanent deformations of the spokes near the nipples so that fast and high amplitude stresses do not occur. going about +30% more tension and then setting back to the goal tension is a rather ancient practice that people don't know about and also don't understand how it works. it all tends to become a blind ritual and that is why crazy things start to propagate, because people don't copy only the good practices but also the bad ones when not knowing how/why things work.
i think i can't stress enough the balancing of radial runout with spoke tension variance for this matter.
and everyone should be able to understand that the chemical factor lowers fatigue limit regardless of maximum (static) spoke tension the wheel remains at.
#44
Senior Member
Dropped it off and made it clear I don't care how it's built other than I want a 2x lacing and I don't want to see bent spokes. He dug up a velo blunt rim. Said it retailed for $90 and discounted it to $60 for my trouble. It's a rim that does not have eyelets, so hopefully the nipples will be able to move freely (Which I pointed out could have been the issue with the other rim as the nipples on that one barely moved). So in about a week, or two I'll get the results. With luck it will last long enough for me to save some money and buy the parts to start building my own wheels.
if you don't care how it's built you should care at least for the final figures... a semitone tension variance and 0.1mm total radial runout would be the mark of a proper job done by someone who is both qualified and patient with his work. and it's very rare to have these figures met without a proper average tension. some settle for twice the variance and radial runout tolerance than i do but this sloppiness has no place for an e-bike.
rims with no eyelets are ok only if with directional drilling (WTB comes to mind).
#45
Generally bewildered
Join Date: Aug 2015
Location: Eastern PA, USA
Posts: 3,037
Bikes: 2014 Trek Domane 6.9, 1999 LeMond Zurich, 1978 Schwinn Superior
Mentioned: 20 Post(s)
Tagged: 0 Thread(s)
Quoted: 1152 Post(s)
Liked 341 Times
in
251 Posts
The CR18 is a widely-used general-purpose rim that receives decent reviews. I can't believe that it would be so intolerant of the small amount of spoke angle shown in the pics. I think that they are not directionally drilled but they should have the holes offset to each side. Are the spokes laced to the proper holes?
There's probably nothing wrong with that CR18 rim on those hubs, provided that one uses butted spokes of the proper gauge, and uses Brandt's time-tested method to lessen the deviation from 90° that the spoke nipple leaves the rim at. For 3 cross I'd use 2.0/1.8 mm (14 and 15 gauge) for drive side and 2.0/1.65 for NDS and front wheel. If there's still some angle, consider using PolyAx nipples.
#46
working on my sandal tan
Join Date: Aug 2011
Location: CID
Posts: 22,629
Bikes: 1991 Bianchi Eros, 1964 Armstrong, 1988 Diamondback Ascent, 1988 Bianchi Premio, 1987 Bianchi Sport SX, 1980s Raleigh mixte (hers), All-City Space Horse (hers)
Mentioned: 98 Post(s)
Tagged: 0 Thread(s)
Quoted: 3871 Post(s)
Liked 2,568 Times
in
1,579 Posts
#47
working on my sandal tan
Join Date: Aug 2011
Location: CID
Posts: 22,629
Bikes: 1991 Bianchi Eros, 1964 Armstrong, 1988 Diamondback Ascent, 1988 Bianchi Premio, 1987 Bianchi Sport SX, 1980s Raleigh mixte (hers), All-City Space Horse (hers)
Mentioned: 98 Post(s)
Tagged: 0 Thread(s)
Quoted: 3871 Post(s)
Liked 2,568 Times
in
1,579 Posts
pressing on the spoke with the fingers hardly achieve anything - near the nipples that is.
you have to press really hard when grabbing parallel spokes at the middle.
for example... you can hardly break a wire when putting some heavy wet clothes at the extremity of the wire but you will be able to i the w tension when you put the load at the middle of it. the same with the spokes being grabbed and pressed to the point when your hands hurt... at the middle of the spoke length.
you have to press really hard when grabbing parallel spokes at the middle.
for example... you can hardly break a wire when putting some heavy wet clothes at the extremity of the wire but you will be able to i the w tension when you put the load at the middle of it. the same with the spokes being grabbed and pressed to the point when your hands hurt... at the middle of the spoke length.
#48
Steel is real
I'd be looking for a new builder
#49
Senior Member
Read my post again, I said “low tension”. Like, not long after you’ve laced the wheel and put in just enough tension to pull the spokes mostly straight. The spokes are still easy to bend by finger at the nipples at that point. I know it works because that’s what I do.
going a very high tension will achieve a more precise bending of the spoke where it's needed. the flexural stress of pressing with your finger will increase tensional stress on the portion of the spoke where it needs to give in and take a different shape by plastic deformation.
i'm not saying it does not work, i'm just saying that there's good reason to do so at low tension and also that there's even more good reason to do so at higher and higher and higher tensions. stress relieving is done in stages. but i am also saying that when going high tension the best results can be achieved.
and i'm saying that some things are to be taken care of (i'll not repeat what i said over and over in recent posts this last week or so) before going high tension like jobst brandt described even without giving a whole explanation for how/why things work and not establishing hard figures for the final spoke tension when lowering back the NDS tension to the final stage.
#50
working on my sandal tan
Join Date: Aug 2011
Location: CID
Posts: 22,629
Bikes: 1991 Bianchi Eros, 1964 Armstrong, 1988 Diamondback Ascent, 1988 Bianchi Premio, 1987 Bianchi Sport SX, 1980s Raleigh mixte (hers), All-City Space Horse (hers)
Mentioned: 98 Post(s)
Tagged: 0 Thread(s)
Quoted: 3871 Post(s)
Liked 2,568 Times
in
1,579 Posts
If you need extreme tensions to build successful wheels, what are you compensating for?